As the global leader in the field of industrial additive manufacturing for ceramics, Lithoz has constantly pushed the boundaries of innovation since its founding in 2011. Based in Vienna, Austria, Lithoz’s mission is to grow ceramic 3D printing as a reliable manufacturing technology for industrial production, and many of our customers are now using additive manufacturing (AM) as an established production method to meet industrial standards. We have become market and technology leaders with a wide range of 3D printers, ceramic materials, and training programs in use worldwide, including in Asia, Australia, and Brazil, while the founding of a subsidiary in the United States has allowed us to better connect with customers and strengthen our global presence.
THE TIME IS NOW—THE GROWTH OF 3D PRINTING
n a world that is becoming ever more digital, ceramic 3D printing is quickly growing into an established production technique. The fact that 25% of Lithoz customers have invested in multiple additive manufacturing systems highlights the success they have had with this technology. They believe AM to be a growing manufacturing market—
and they are not the only ones. A recent SmarTech Analysis study showed that the additive manufacturing industry is expected to grow over the next decade to become a
$4.8 billion market by 2030,
1 with the area of technical applications representing the most significant sector for driving market growth to more than $3 billion. The adoption of ceramic AM is expected to rapidly increase, with the main inflection point being in 2025 as major ceramic AM technologies come to maturity and benefit from having enough of a presence in the market to support the serial production of final components. Figure 1 shows growth trends expected for materials and applications.
2
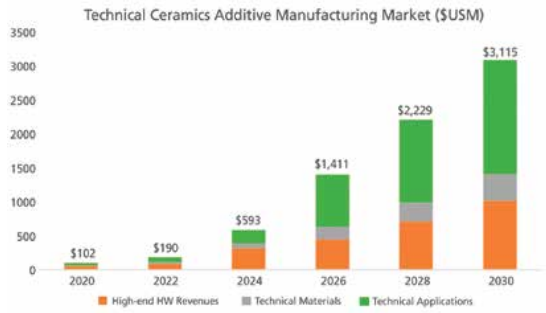
Figure 1. The rapid growth of the technical ceramics market in 3D printing. (Reference 2)
Credit: Anusci, 3D Printing Media Network
Many early adopters of ceramics AM are now up to eight years ahead in terms of AM experience, giving them a significant business advantage, while the fact that customers are now using 3D-printed parts means that suppliers offering 3D printing are quickly surpassing those who do not. Finally, as the technology becomes more well-known, the
range of applications is broadening—new players in various fields are entering the ceramic AM market, finding new applications in the process and innovating past traditional ceramic companies. This innovation puts them at a great advantage, allowing them to explore new design ideas and functionalities unachievable using conventional forming techniques.
Additionally, additive manufacturing gives businesses a secure supply chain in a way other production methods simply cannot. This independence has made AM invaluable for many companies during the pandemic, as they could be self-reliant in times of economic and manufacturing uncertainty. The entire AM method is modeled after digital independence—once a customer has a digital file of the part, components can be produced and edits made to reach certain parameters, and files can be saved and accessed anywhere in the world. Where there is a 3D printer, this part can now be produced. The use of digital files opens up an entire digital warehouse for the customer, making it easy to gain new connections and innovate with others in their field.
Ceramic 3D printing is very well suited to modern manufacturing and development, no matter what field a company is based in, and the market will grow rapidly as more businesses implement AM as a serial production method to find new, innovative applications and enjoy the advantages of digitalization and a stable supply chain.
THE ADVANTAGES OF CERAMIC 3D PRINTING
As we have seen, ceramic additive manufacturing will undergo a huge period of growth in the next decade as customers take advantage of 3D printing technologies, making huge waves in the manufacturing market and disrupting traditional manufacturing processes. However, when considering the fact that there are already many well-established and conventional manufacturing methods available for ceramics, the question is: Why is another technology needed?
The reason lies in the development of today’s increasingly complex and customized applications. Customers demand ever more from their technology and, as manufacturing environments develop further, demand grows for more complex components to be rapidly produced, while new ideas for applications require more freedom in design to be made a reality (Fig. 2).

Figure 2. Lithoz 3D-printed silicon nitride. Ceramic 3D printing can print parts that might be too costly or impossible to produce using traditional manufacturing. Credit: Lithoz
When it comes to conventional forming methods, such as milling, pressing, and injection molding, companies are often limited to designing parts that can be produced, instead of parts they want to produce. The design freedom offered by 3D printing is, in this area, simply unparalleled, allowing designers to focus more on functionality
when coming up with new concepts. As Ing. Tassilo of Fraunhofer IKTS states, the manufacture of “extremely complex-shaped or individualized components ... has primarily been occupied by AM” so far.3Using AM, it is possible to construct unique geometries, unachievable using traditional methods, and this ability greatly expands the range
of possible applications for businesses in all fields. As such, Lithoz’s ceramic 3D printing is an enabling technology for customers that can keep pace with even their most innovative ideas. While conventional technologies have reached their limits in terms of fulfilling modern aims, AM has grown and become a strong industry that can be used
for such projects.
Another reason for implementing AM is the fact that this technology greatly speeds up the entire product development process, resulting in a shorter time to market. Design changes can be made more quickly and easily, which encourages the improvement of existing products, while the rapid production of prototypes facilitates entry into new markets. The speed of the entire process enables a quick start to exchanges between businesses and potential customers. Trend forecasters predict that customers in the future will want technology that facilitates hyper-customization, meaning that products can be rapidly altered without complication. Using AM, new designs can be created without losing the original form simply by altering digital files. This opportunity is a great one for companies to use AM to extend or change their business models and enable profitable mass customization.
One significant advantage of AM is that it does not require any set-up costs. The tooling required for traditional manufacturing processes not only has a negative impact on a part’s time-to-market, but also makes such processes costly for small- or medium-sized production runs. AM technology makes small- and medium-sized runs more economical, while the fact that customers can use AM to specifically customize their designs enables easy improvements and further innovation in product design, as customers have no cost or time worries.
Take this electrosurgical tool (Fig. 3) as an example. Used in precise medical applications, this component is characterized by its extremely small size, complex internal geometry, and challenging features—aspects which are very difficult to achieve using traditional molding technologies, and which would require expensive and time-consuming tooling. However, as tooling is not required using AM, this part can be produced quickly and economically, while still ensuring that the exact form requirements are met.

Figure 3. Lithoz is known for its high-resolution and accurate technology, which is trusted for even the most precise of applications, such as these surgical tool components.
Credit: Lithoz
HOW CERAMICISTS CAN LEVERAGE THEIR KNOW-HOW WHEN SETTING UP 3D PRINTING PROCESSES
In terms of materials, ceramicists are at a great advantage when implementing AM. This advantage is due to ceramic AM being very similar to other ceramic manufacturing processes—in terms of actually implementing 3D printing, thermal post-processing is essentially unchanged. Only the product designs need reworking, and prior ceramic experience and knowledge can still be used for the second step of the process. Furthermore, 3D printing gives ceramic businesses another option when it comes to forming technologies. Ceramics are known as being rather difficult to process in comparison to other materials, and having a new forming process alongside machining or pressing enables new ceramic applications. By adopting 3D printing, ceramicists put themselves at a great advantage to beat competitors still solely using conventional forming methods, and they can now work with difficult-to-process materials such as silicon nitride.
Overall, ceramic industries can greatly benefit from implementing AM. This technology can be used as a single manufacturing platform for everything from prototyping and small-batch production up to mass manufacturing, opening the door to a myriad of manufacturing possibilities that businesses may not have had access to before.
At Lithoz, we have already seen the success with which many different companies have implemented ceramic additive manufacturing into their production environments and how they have been able to innovate even further as a result. One company that has already taken advantage of AM is technical ceramic producer Ceramco (Fig. 4), who has been working with Lithoz’s technology since 2015 and has doubled its 3D printing production capability. Thomas Henriksen, president and CEO of Ceramco, describes how the company originally implemented AM for cheaper prototyping before realizing its full potential: “Since we make parts by ceramic injection molding (CIM), we initially thought 3D printing would be a good way to give customers prototypes if they didn’t want to pay for any CIM tooling. However, it turned out that many additive customers remained as additive customers, and seldom went to serial production that required CIM.
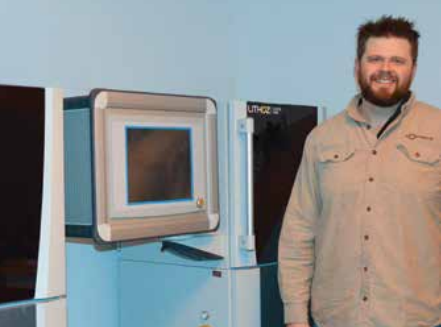
Figure 4. President and CEO of Ceramco Thomas Henriksen stands with the Lithoz 3D printer CeraFab 7500. Credit: Ceramco
After seeing the success of AM with businesses, Ceramco decided to invest in this technology. “More often than you might think, customers persistently want additively made parts, even over conventionally made parts,” Henriksen says. As leading ceramic part producers, Ceramco’s experience has been that “with the right parts of ideal sizes, Lithoz 3D printing technology can be used to make very good quantities.”
As Ceramco was so far ahead of the curve in terms of investing in this technology, it is well-trained in working with this process. “We were considered an early adopter by purchasing our first machine in 2015, long before any other technical ceramic manufacturers in the U.S. invested in a machine,” Henriksen says. Early investment in additive manufacturing allowed Ceramco to innovate beyond other ceramic companies, becoming leaders in the field and benefiting from the economical and effective aspects of 3D printing.
HOW AM IS DRIVING INNOVATION IN MULTIPLE MARKETS
It is now clear that AM excels in applications where injection molding, milling, and pressing cannot. But where are businesses benefiting the most? It is areas such as medical devices, the semiconductor industry, machinery, electronics, and dental components that are most driving the growth of ceramic 3D printing. Ceramco found that since AM
allows for the printing of such complex structures, this technology encourages and enables the production of interlocking ceramic components that contain more features than an injection molded part. Such parts can have multiple functionalities in varying industries, thus benefiting the entire ceramic industry and meaning that components “are not necessarily market specific.” Henriksen believes that ceramic AM “will give people access to ceramics much more readily, which I think will spur innovation in finding new applications.”
AM has great uses in the aerospace and industrial gas turbine industries, where the freedom offered is being used to develop new designs for casting cores with more complex structures than ever before, including multiple walls and fine branches (Fig. 5). These new forms cannot be produced using conventional injection molding methods, showing how AM has greatly expanded applications in this area in ways that other technologies could not.
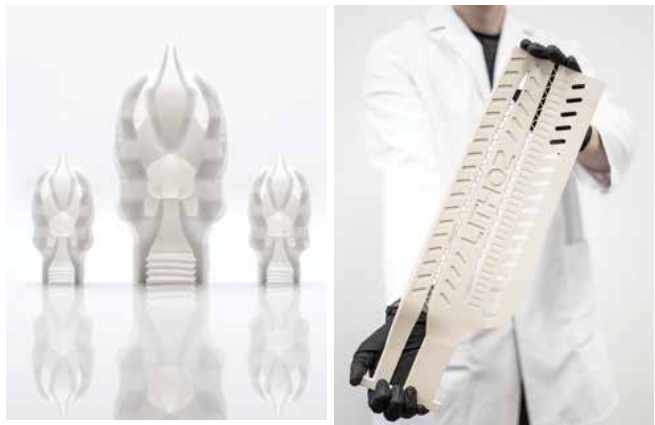
Figure 5. From small, complex parts such as aerospike nozzles (above) up to much larger industrial components such as casting cores (right), AM can produce near limitless geometries. Credit: Lithoz
Developments in AM opened the door to applications far beyond technical parts. It is now possible to manufacture components for medical and dental applications, with the material properties of ceramics coming into their own in terms of biocompatibility. Additive manufacturing is being used to serially produce surgical tools in lot sizes of up to 10,000 parts, while dental parts and bone implants can be efficiently produced and expertly customized simply by editing the digital file. This ability means that medical components and implants can be matched to individual patients and certain properties modified to best suit the situation. In these fields, CE-certified Medical Devices
(Class III) and FDA-approved Medical Devices (Class IIa) have already been successfully produced, used, and implanted in vivo.
Redesigning allows for improvements and new products to become fully customizable, while the entire process is made more economical and cost-effective due to the material-saving and toolfree characteristics of AM. As a result, it is clear that while companies may not currently consider themselves to be suited to AM,
it only takes a few small changes to start taking advantage of this innovative technology.
THE SWITCH TO 3D PRINTING—HOW TO GET THE MOST OUT OF THIS GAME-CHANGING TECHNOLOGY
While the implementation of AM requires relatively few changes, adopting a wholly new manufacturing process does, of course, require patience and can pose challenges in terms of mindset changes. Having an experienced partner is a key element in the optimal integration of AM into existing processes and structures. Having worked with many customers across research and industry, Lithoz understands the importance of supporting new and existing AM adopters and has therefore tailored its business model to support clients all the way from initial adoption to eventual scale-up. We offer our customers an experienced support service that enables them to seamlessly integrate our ceramic 3D printing technology and, when the time comes, implement scale-up capabilities for serial production.
In May 2020, Lithoz opened the Lithoz Innovation Lab (LIL, Fig. 6) for this precise purpose—to advance ceramic 3D printing and enable businesses to accelerate their developments and further innovate in ceramic manufacturing. Alexander Michaelis of the Fraunhofer Institute for Ceramic Technologies and Systems IKTS gave his opinion of the new space: “This new state-of-the-art facility is a huge leap forward, as it gives industry and R&D the opportunity to push the limits of ceramic 3D printing, while making discoveries along the way.”
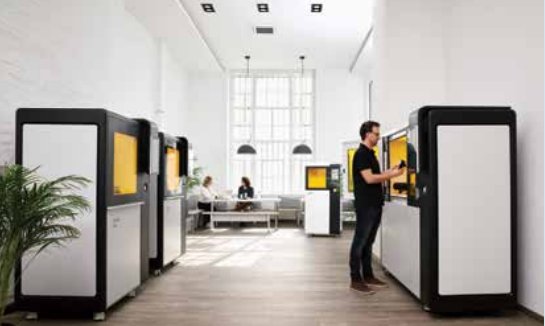
Figure 6. The newly opened Lithoz Innovation Lab. Credit: Lithoz
By ensuring that businesses are fully using AM for their industries, we are helping the growth of the AM market as an established manufacturing technology. Johannes Homa, CEO of Lithoz, says, “We see ourselves not only as a machine supplier, but as a partner for our customers. We have learned that a partnership approach is the key to successfully implement ceramic AM. AM has already made huge waves in many industries, and we at Lithoz are looking forward to seeing the new applications this technology will offer and where it will take us in the years to come.”
ABOUT THE AUTHORS
Alice Elt is a content specialist and Isabel Potestio is a business development and sales manager for Lithoz GmbH, Vienna. For further information, contact Isabel Potestio at ipotestio@lithoz.com.
REFERENCES
1 SmarTech Analysis. “Ceramics additive manufacturing production markets: 2019–2030.” https://www.smartechanalysis.com/news/smartech-analysis-2020-report-on-ceramics-additive-manufacturing-highlights-new-dynamics-within-potential-4-8-billion-market-by-2030
2 Anusci, V. “New market report highlights $3.1 billion technical ceramics opportunity by 2030.” 3D Printing Media Network, 22 April 2020. https://www.3dprintingmedia.network/new-report-on-ceramics-additive-manufacturing
3 Ing. Tassilo Moritz. “Ceramic injection moulding: Developments in production technology, materials and applications.” Powder Injection Moulding International, Vol. 14 No. 4, December 2020, p. 62